Notes on Brass and Bronze
I often find myself explaining these metals on an individual basis, so this note provides an opportunity to do so to a number of people at the same time. It’s not a comprehensive guide, but one where I’ll cut an awful lot of technical corners in order to (I hope) provide a useful insight. The usual trouble is there are so many types of copper based alloys that even the most hardened copper nerd tends to glaze over when presented with all the variants. For the most part, then, I’m just going to use the words “brass” and “bronze”. Also, because many brasses and bronzes can be cast, I’m going to deal almost entirely here with materials and processes to do with fabrication.
What are these Metals?
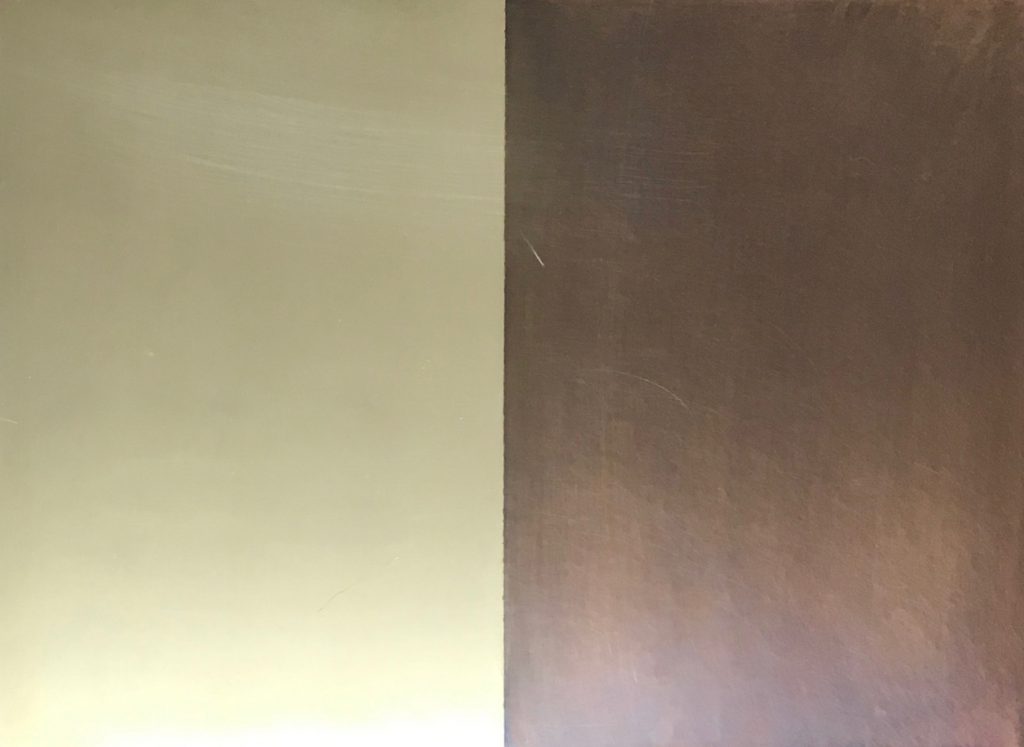
Brass is an alloy of copper and zinc – typically 60% copper/ 40% zinc. Copper being reddish in colour, and zinc being silver, means you end up with the characteristic yellow colour of brass in it’s natural state.
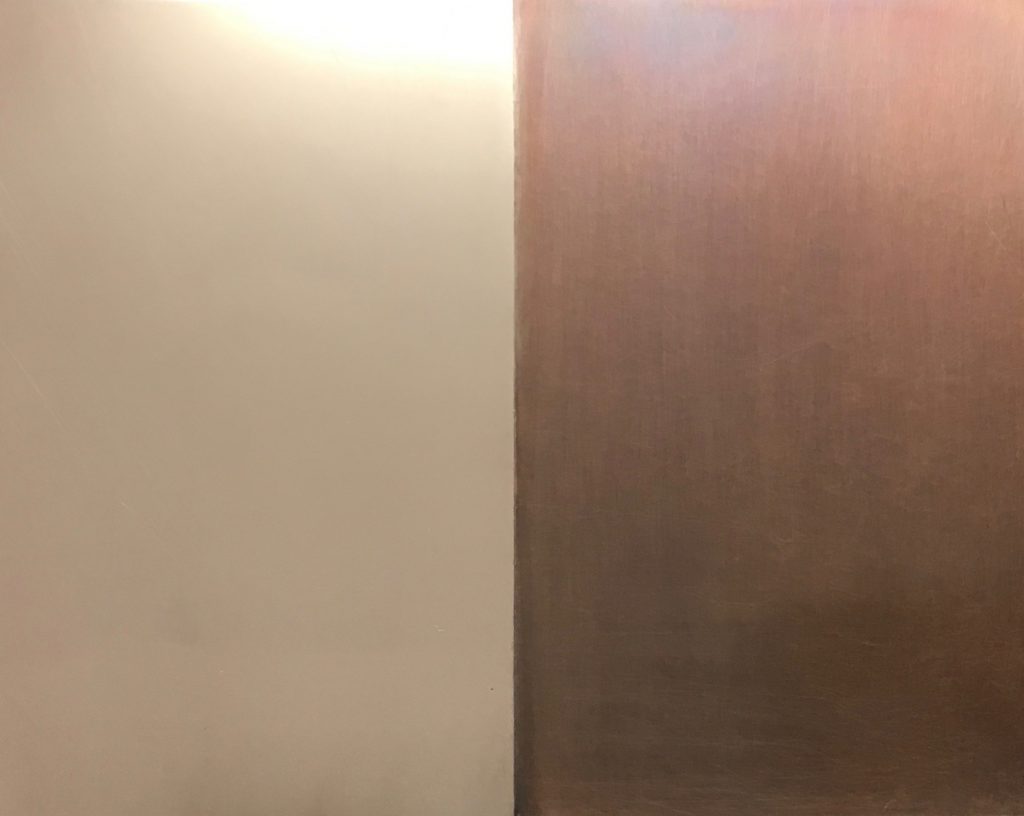
Bronze is copper mixed with other alloying elements. In the alloys used most often tin is involved in amounts of maybe 5-8%. So you get a material which looks more like copper – red-gold rather than yellow-gold.
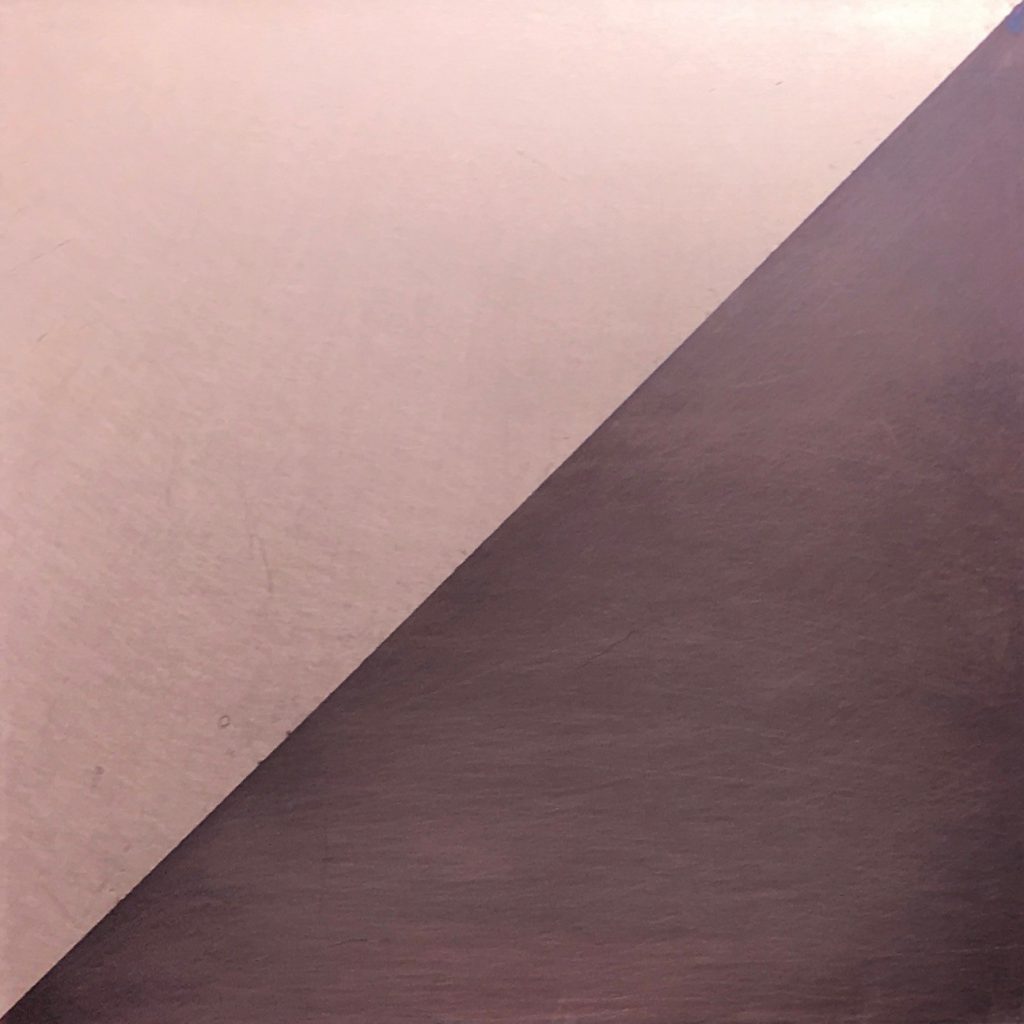
Copper is expensive, tin is expensive, but zinc is relatively cheap – so this affects the cost. Bronze is nearly twice the price of brass and both are expensive when compared to steel; roughly 5 and 10 times the price for brass and bronze respectively.
Thing #1 – using lots of bronze (or brass) is likely to be costly – in my experience it often gets “value-engineered” out of a project if specified indiscriminately.
How can you buy them?
Brass can be had in a wide variety of rod, tube, sheet, flat bar, and extruded sections (like angle, T and channel sections). It is also possible to have sections made – so long as you want more than a few hundred kilos of it. But it’s not an infinite variety of sections – so it is worth checking which ones exist before specifying. Just to complicate the issue, brass sections are often made in inch sizes, which confuses the hell out of most people younger than 50.
Bronze is available in rod, sheet and flat bar, and that’s about it. It does not extrude well (so you can’t get sections like angles, T’s and so on). But what about “architectural bronze” handrails and things like that? Sorry, but…….
Thing #2 - There is no such thing as “Architectural Bronze” - it is almost always patinated brass
I don’t know how this has arisen, but you simply can’t go to a metal factor and ask for architectural bronze. What may be confusing the issue here is that there is a type of brass sometimes referred to as “manganese bronze” which is better than brass at corrosion resistance, so resembling bronze in that way, but which does extrude well. So it is quite often used very effectively for handrails and window frames. But despite the name it is brass, as will be any extruded sections. For the most part “Architectural Bronze” is brass patinated to look like bronze. We’ll look at patination later.
How can this stuff be joined together?
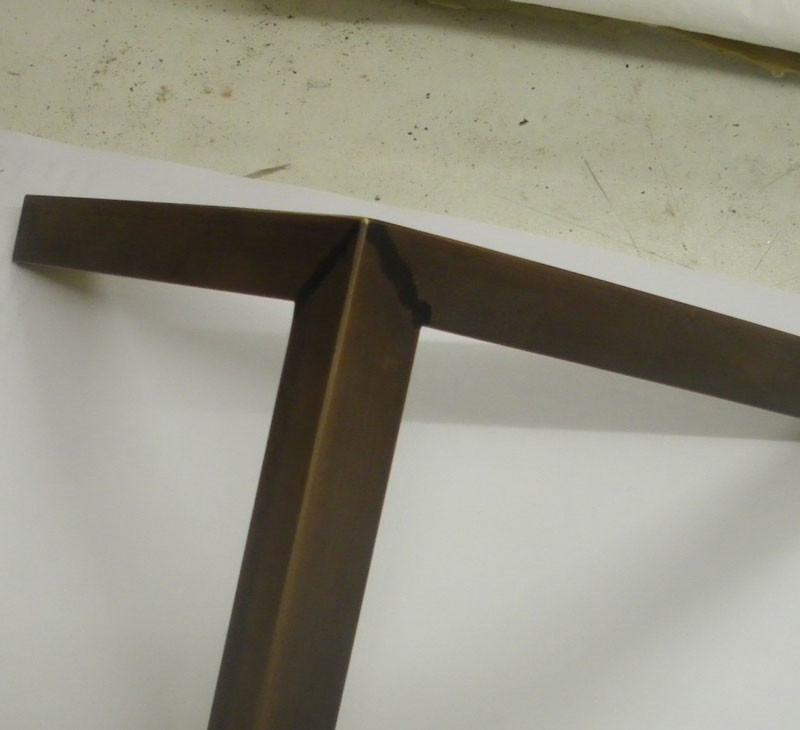
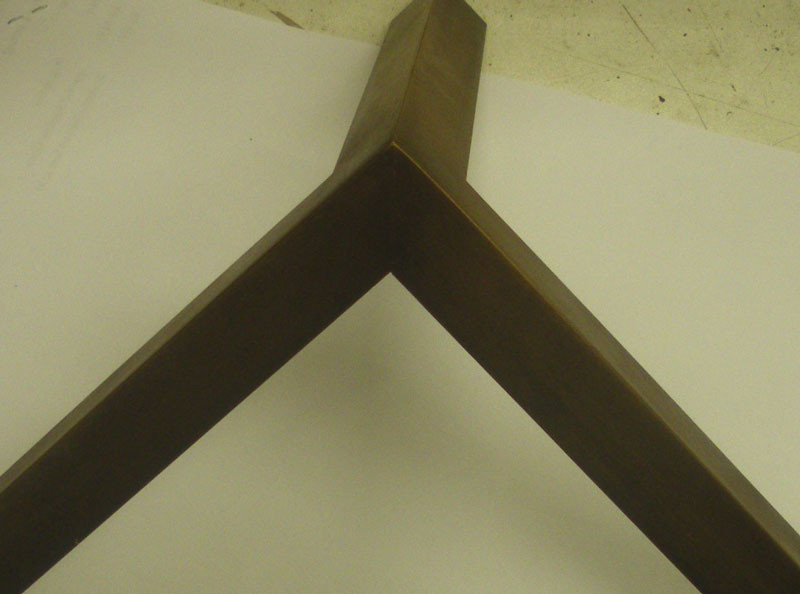

Brass can be welded, but
• it’s not a particularly strong join, and
• if you want to patinate it afterwards, the join always shows, and
• it does distort readily around the welds
The reason for all of these issues is down to the nature of the metal (approximately 60 copper, 40 zinc). Copper has a much higher melting point than zinc, so when you weld it, the zinc comes out of the alloy in a puff of white smoke, which changes the alloy around the weld area (hence different colour patination, and distortion) and creates a brittle zone just beyond the weld area (hence not very strong). If the final finish is polished, then it doesn’t show so much, but otherwise we try to hide the welds, for example inside a frame, and have a hairline join on the visible side.
The pictures show the options for welding
Sometimes we are asked to braze brass – but brazing is brass welding (when used on steel for example) so for brass it’s just welding. Specifications quite often call for braised joints. Braising is what you do to slow-cook cheap joints of meat, brazing is brass welding of metals.
Brass can be silver soldered, which reduces the distortion, but unless the final article is polished, and the joints very tight fitting, you’ll be able to see the join. If patinated the join shows badly.
Brass can also be soft-soldered, but that is decorative only, and you have the same issues if you want to colour the material. All of which leads to
Bronze can be welded using a filler of similar composition to the basic material, and though tin also has a much lower melting point than copper, there is less of it to escape. The weld is strong, and nearly invisible whether the item is self colour, polished or patinated. This means that you can make structural elements from bronze, whatever finish you choose. But, as mentioned above you are more limited in the sections and shapes available to start from, in particular there isn’t very much tube available, and bronze is about twice the price of brass.
Thing #3. If you want an effective structure in brass, then mechanical fastening (bolts etc) is your best bet. This also applies to architectural bronze.
Thing #4. If you want to end up with invisible joints in a patinated brass component, then either mechanical fixing, or hidden welds are your best options, though very dark patination can nearly match the weld area. Again this also applies to architectural bronze.
Thing #5. You can make seamless welded structures in bronze – but they'll be expensive and/or heavy.
Cutting, forming and shaping
With widespread use of CAD software and CNC machines, the most common way to cut shapes from sheet is to use either laser cutting (up to about 3mm at the time of writing) or waterjet cutting. I’m not sure of the maximum thickness for waterjet, but I know it is at least 25 mm.
Brasses and bronzes are readily machined (well, the more common alloys anyway), and engraved.
An area which sometimes disappoints is folding sheet. If a sheet is folded, then the tightest available inside radius is going to be about the same as the material thickness, which means the outside radius will be about twice the material thickness. So for example a 1.5 mm sheet (typical for counter top or cladding) will end up with an outside edge radius of 3mm if folded. You can get sharp edges by joining sheets together – but there is almost certain to be distortion if a long edge – or by using an extrusion, or by gluing sheets to a substrate of some sort, or by machining from solid (an unlikely option).
Thing #6. Sharp edges are easier to draw than to make from sheet – and anyway may not be desirable if people are going to bump into them.
Finishes & Maintenance
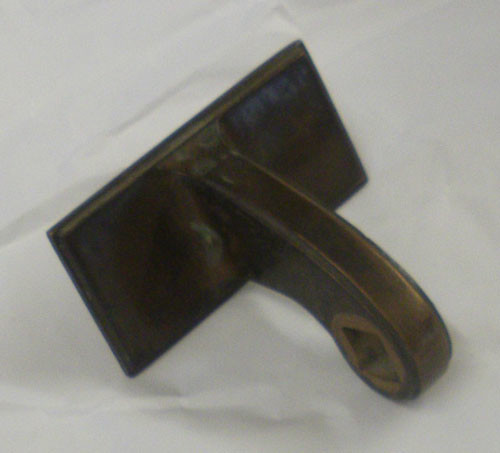
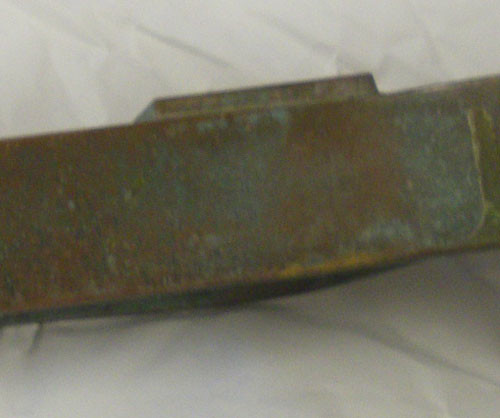
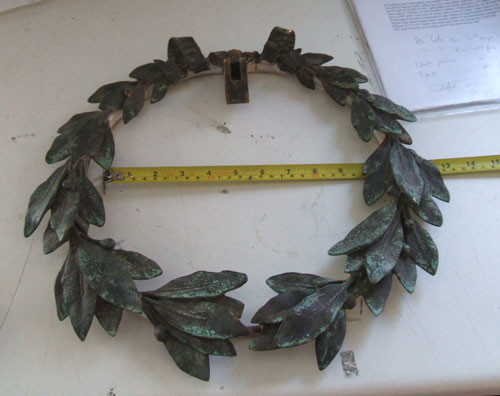
It’s probably fair to say that as an engineer, I worry about things hanging together and working, whereas designers and architects worry more about appearance. Given that both things have to be to everyone’s satisfaction, that’s fair enough. Left to their own devices, brass and bronze will darken and discolour over time. The resulting oxide might look “dirty” but is in fact very effective at killing bugs and bacteria, so in fact it’s quite hygienic.
The main options for finishing these metals are:
A brush finish which can be either a grained satin finish, or a swirly pattern from an orbital sander. Both provide a matt finish which looks well and is usually fairly easy to achieve. The snag is that they mark very easily from finger prints and other pollutants. After a time a natural patina will build, so that the often touched parts become light, where the rarely touched parts darken, and this can look very handsome. But the transition period is very messy, and few people admire the look while it’s happening. However it is straightforward to restore to a bright finish with scouring pads.
You can use protective coatings like wax or lacquer. Wax has the advantage that if a part discolours or gets wet, it is easy to rub it back and re-wax. Lacquer is more hard-wearing, but if it does scratch (or if water gets underneath) you end up with a speck or scratch of discoloured material, and then face the task of getting all the lacquer off to re-coat. I heard that lifeboat crews use clear nail varnish as lacquer on their brass and bronze fittings, not because it is particularly good, but because it is easy to remove with nail varnish remover.
A polished finish is more difficult (= expensive ) to achieve, but is better at resisting marks like fingerprints, and can be maintained by polishing. It doesn’t provide a very good key for lacquer or varnish, and as with brushed finishes if that kind of coating breaks then ugliness follows.
Thing #7 Self colour brushed or polished finishes look well but usually need maintaining
Patination can take all sorts of forms. As mentioned above these materials will patinate naturally, ending up black or brown or green depending on the local conditions (salt-laden, heavy road traffic, industrial pollutants, foot traffic, being handled etc). The photos show a few examples.
A recurring problem with designers of all flavours is that most aren’t comfortable with a surface colour that designs itself. So we are often asked for a particular shade (usually of brown) as if it were a paint chart. The problems are that patination is a process whose results are inevitably variable. In practice the result will be influenced by the temperature and humidity when the patination was done, the surface treatment following patination, how long it has been there, and the conditions it has had to endure in the meantime. On some occasions we are asked to match a patina that has been around for decades. The snag is if we match it today, what will it the new one be like in 10 years time? How will the old one have developed in that time? And so on.
The “standard” patination is a mid to dark brown – sometimes referred to as “old penny brown” or BMA (Brass made antique?). However there are a number of specialists in patination who can create all sorts of patterns and colours, so you don’t have to be stuck with brown.
Thing #8 Patination isn't paint – it will vary across a component and over time.
Thing #9 Patination doesn't have to be brown.
Plating
Plating goes very well onto these metals – common choices being nickel (bright or brushed) and gold, but again there are plenty of variations available. Two things to bear in mind, though. Firstly plating – particularly bright nickel or chrome – highlights the slightest defects, many of which would be imperceptible if finished polished or patinated. Occasionally we have been asked to refurbish an old piece, and then plate it. I don’t think it has ever lived up to the expectations of the client. Secondly plating does not adhere well to very sharp edges, so they need to be softened if the plating is to last. I reckon on at least 1mm radius. The good thing about plating is that the finish lasts a good long time, and can be removed by the same process in reverse. The limitations tend to be to do with the maximum size of tank available for plating. Also beware of plating components made from a number of tubes – electrolyte can seep into the tubes, and then spend the next few days and weeks seeping out again, so spoiling the plated surface.
Thing #10 Plating adheres well to brass or bronze, but highlights any defects, and hates sharp corners
Protection
So what can you do to protect the finish? Well I think the first point to re-state is that these materials will create their own protection if left to their own devices. Unlike steel where an oxide forms (rust) and then falls off to expose new metal, the oxides on yellow metals are hard-wearing and long lasting. The problems come if you don’t like the colour (or the green dribbles from the statue onto its plinth). I suppose it depends on circumstance, but for my money lacquer should only be used if there is a negligible chance of the item touching other items or being handled, maybe a picture frame for example. A polished finish can be maintained by polishing, but that is a regular maintenance task. A patinated finish can be left to itself – handling or footfall will change the appearance as in the rails and treadplates in tube stations, as will air pollution for statuary. In effect patination merely mimics the first few years of service, from which the colour and texture develops itself over the next few decades. But paint it ain’t, and it won’t stay the same colour over time.
Thing #11 Lacquer/varnish is only a good choice where an item is unlikely to come into contact with anything except air.
Thing #12 Patination can be left to its own devices to develop naturally over time. If required, wax or oil can maintain the colour longer for parts which aren't regularly handled (eg statuary).
Alternatives – other things are available
Paint will stay the same colour, and there are plenty of metallic paints which mimic bronze and brass. It’s not as characterful as the real thing, but since you can use a much cheaper substrate like steel or aluminium, it may be a good choice, particularly if you want to create a structure. Plus you can get touch-up kits for cut edges and/or scratches.
Or you can get treated metals – there is for example a range of bronze effect stainless steel sheets (typically 0.8 to 2mm thickness) which are good for cladding, and whose coating is remarkably tough. I made some trims where this metal needed to be folded back on itself, and the coating showed no signs of cracking. Not only that, it stains with fingerprints just like the real thing!
Finally there are the liquid metals. Usually a resin with a very high proportion of powdered metal, these can be moulded or poured, sometimes combined with other shades or colours to create amazing effects. Depending on the composition, the surface can be cut back, patinated or over coated with clear resin. It is however just a surface treatment – not itself structural.
Summary - Twelve things about Brass and Bronze
1. Using lots of bronze (or brass) is likely to be costly – it often gets “value-engineered” out of a project if specified indiscriminately.
2. There is no such thing as “Architectural Bronze” – it is almost always patinated brass
3. If you want an effective structure in brass, then mechanical fastening (bolts etc) is your best bet. This also applies to architectural bronze.
4. If you want to end up with invisible joints in a patinated brass component, then either mechanical fixing, or hidden welds are your best options, though very dark patination can nearly match the weld area. Again this also applies to architectural bronze.
5. You can make seamless welded structures in bronze – but they’ll be expensive and/or heavy.
6. Sharp edges are easier to draw than to make from sheet – and anyway may not be desirable if people are going to bump into them.
7. Self colour brushed or polished finishes look well but usually need maintaining
8. Patination isn’t paint – it will vary across a component and over time.
9. Patination doesn’t have to be brown.
10. Plating adheres well to brass or bronze, but highlights any defects, and hates sharp corners
11. Lacquer/varnish is only a good choice where an item is unlikely to come into contact with anything except air.
12. Patination can be left to its own devices to develop naturally over time. If required, wax or oil can maintain the colour longer for parts which aren’t regularly handled (eg statuary).
Feel free to use this – ideally with some acknowledgement
Moray MacPhail 2018
BronzeWork, Unit 15, Martlesham Creek, Sandy Lane, Woodbridge, IP12 4SD +44 (0)7305 426495 moray@moraymacphail.com
BronzeWork, Unit 15, Martlesham Creek, Sandy Lane, Woodbridge, IP12 4SD
+44 (0)7305 426495 moray@moraymacphail.com